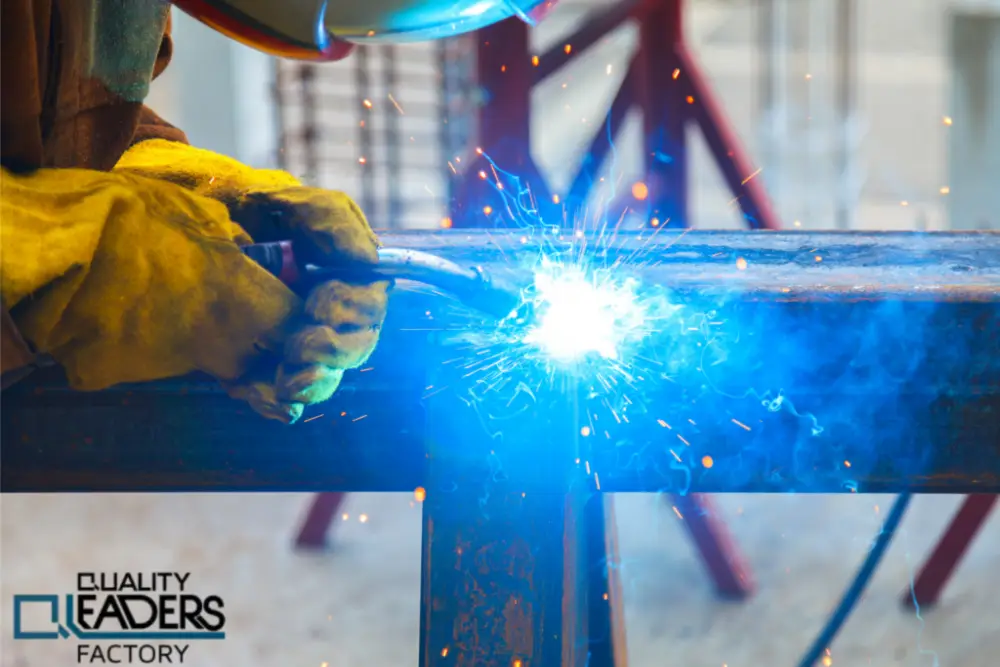
What is Steel Fiber? Redefine Your Structural Integrity
Introduction:
Steel fibers mixed into concrete offer an alternative to traditional steel bars or welded fabric in specific applications. While the concept has existed since the late 19th century, it gained momentum in the 1970s, particularly in Europe, Japan, and the USA. Steel fiber reinforcement has since found widespread use in industrial floors, pavements, external paved areas, sprayed concrete, composite slabs, and precast elements.
Over the last ten years, steel-fiber-reinforced slabs have been erected in millions of square meters throughout Saudi Arabia, primarily for pile—and ground-supported floors. Because they need less traditional reinforcing, these fibers replace standard steel fabric in ground-bearing slabs and even in suspended ground-floor slabs on piles. This can help save money.
Additionally, using steel fibers can enhance safety by reducing the handling of heavy reinforcement materials and preventing issues associated with the misplacement of conventional steel within the slab depth.
What is Steel Fiber?
Steel fibers are tiny, filament-like materials manufactured from different grades of steel. These fibers are typically added to concrete mixes to enhance their tensile and flexural strength, toughness, impact resistance, and fatigue performance. Incorporating steel fibers into concrete creates a composite material that exhibits superior properties to conventional reinforced concrete.
Modern concrete buildings require the use of steel fiber reinforcement, which gives concrete structures increased strength, longevity, and crack resistance.
Steel fibers are small, discontinuous, and uniformly distributed fibers made from various types of steel. They are typically added to concrete mixes to improve their mechanical properties.
Manufacture of Steel Fiber
Steel fibers are produced through various processes, including cold-drawing, cutting, or slitting steel rods or sheets into smaller lengths. The type of steel used in manufacturing steel fibers varies, with common materials including carbon steel, stainless steel, and galvanized steel. Each type of steel offers different mechanical properties, corrosion resistance, and cost considerations, allowing for tailored solutions to specific project requirements.
Types of Steel Fiber:
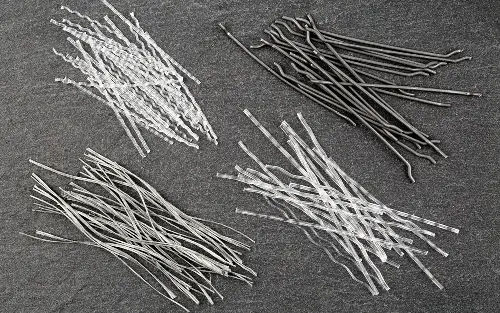
- Hooked End Steel Fibers:
These fibers feature a hooked-end design, which enhances their bonding with concrete and improves the composite material’s mechanical properties.
- Straight Steel Fibers:
Their unique characteristics are their smooth surface and the regular shape of straight steel fibers. They provide reliable reinforcement and are often preferred for applications with a smooth finish.
- Crimped Steel Fibers:
Crimped steel fibers have a wavy or corrugated profile, which increases their interlocking capability with concrete, enhancing bond strength and overall performance.
- Slit Sheet Steel Fibers:
Slit sheet steel fibers are manufactured by slitting thin sheets of steel into narrow strips. These fibers offer high aspect ratios, making them particularly effective in reinforcing concrete.
Exploring Different Types of Steel Fiber for Concrete
When it comes to reinforcing concrete, steel fibers are like the secret ingredient that adds strength and resilience to the mix. But did you know there isn’t just one type of steel fiber? There are a few varieties, each with unique properties and perks.
Let’s dive in and check them out:
1. Hooked End Steel Fibers:
Picture tiny pieces of steel with little hooks at the ends. These bad boys are all about anchorage. They dig into the concrete matrix, making sure they stay put. That means better bond strength and more flexibility, which is handy for things like industrial floors and tunnel linings.
2. Straight Steel Fibers:
Unlike their hooked cousins, straight steel fibers keep things simple. There are no fancy hooks here, just uniform lengths of steel. They’re excellent for increasing concrete’s flexural and tensile strength, so don’t let their simplicity deceive you. Think pavements, precast elements, and bridge decks that need extra muscle.
3. Micro Steel Fibers:
Now, imagine steel fibers on a diet. Micro steel fibers are super thin, but don’t underestimate them. Though they are tiny in size, they are incredibly durable and robust. They’re perfect for thin-section applications, overlays, and high-performance concrete mixes where you need strength without adding bulk.
The Steel Fiber Manufacturing Process: A Closer Look
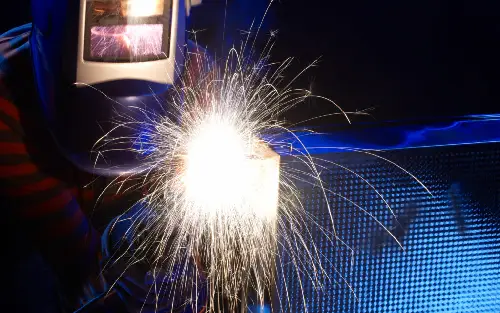
Have you ever wondered how those tiny but mighty steel fibers, crucial for reinforcing concrete, are made? Let’s take a look behind the scenes at the intriguing world of producing steel fiber.
Step 1: Raw Material Selection:
It all begins with selecting the right steel material. Quality is key here. Think strength, flexibility, and corrosion resistance.
Step 2: Cold Drawing or Slitting:
Now, it’s time for some transformation. There are a couple of ways to shape steel into fibers. One standard method is cold drawing. Consider passing a steel rod through a sequence of dies that cause it to progressively become thinner and longer until it becomes a fine fiber and HVAC components. Another method involves slitting steel sheets into narrow strips. Both methods achieve the desired result: individual steel fibers ready to reinforce concrete.
Step 3: Surface Treatment (Optional)
Sometimes, steel fibers get a little extra pampering. Surface treatments like galvanizing or coating might improve corrosion resistance and enhance bonding with concrete. It’s similar to adding a layer of defense and resistance to these fibers.
Step 4: Packaging
Once the steel fibers are prepped and ready, they’re packaged for their journey to concrete production facilities. Bags or containers keep them safe and sound until they’re ready to work their magic in concrete mixes.
And there you have it – the steel fiber manufacturing process! From selecting top-notch steel to shaping, treating, and packaging, every step ensures these tiny reinforcements are primed and ready to strengthen concrete structures worldwide. It’s a testament to the blend of craftsmanship and science in creating materials that build our modern world.
Properties of Steel Fiber:
Tensile Strength:
Steel fibers possess high tensile strength, which enables them to distribute tensile forces within concrete, effectively preventing crack propagation.
i) Ductility:
The malleable nature of steel fibers allows them to deform without fracturing, enhancing concrete’s ability to withstand applied loads and deformations.
ii) Aspect Ratio:
Steel fibers’ aspect ratio (length-to-diameter ratio) plays a crucial role in determining their effectiveness. Longer fibers generally offer better reinforcement than shorter ones.
iii) Corrosion Resistance:
Properly manufactured steel fibers are designed to resist corrosion, ensuring the long-term durability of reinforced concrete structures.
iv) Bonding:
Steel fibers are engineered to bond securely with concrete, providing robust reinforcement throughout the material.
Applications of Steel Fiber:
- Industrial Flooring:
Industrial flooring applications frequently use steel fiber-reinforced concrete (SFRC) because of its resistance to abrasion, impact, and significant loads.
- Tunnel Linings:
SFRC is employed in tunnel linings to enhance structural integrity and provide resistance against cracking and deformation caused by ground movements and environmental factors.
- Precast Concrete Elements:
Precast concrete components, including panels, beams, and pipes, are produced with steel fiber. This reinforces their strength and longevity.
- Bridge Decks:
Steel fiber-reinforced concrete is increasingly used in bridge deck construction to improve structural performance and extend service life, particularly in areas prone to corrosion and deterioration.
- Shotcrete Applications:
Steel fibers are incorporated into shotcrete mixtures to enhance the mechanical properties of sprayed concrete, making it suitable for various applications, including slope stabilization and tunnel support.
FAQs:
How strong is steel fiber?
The strength of steel fiber can vary depending on several factors, such as the type of steel used, the manufacturing process, and the dimensions of the fibers. Generally, steel fibers have high tensile strength. Steel fiber is exceptionally strong, with tensile strengths typically ranging from 1000 MPa to 3000 MPa or higher, depending on the specific type and manufacturing process. This high tensile strength enables steel fibers to effectively reinforce concrete, enhancing its overall stability, toughness, and resistance to cracking.
What is more potent than steel fiber?
Carbon nanotubes (CNTs) are more vital than steel fiber. These cylindrical carbon structures exhibit exceptional mechanical properties, including extremely high tensile strength and stiffness. Despite their tiny size, carbon nanotubes can be significantly more robust than steel on a per-weight basis, making them a promising material for advanced reinforcement applications in various industries, including aerospace, automotive, and construction.
What are the disadvantages of steel fibers?
Despite their benefits, steel fibers also have some disadvantages:
- Cost:
Steel fibers can be expensive compared to traditional reinforcement methods, impacting overall project costs.
- Corrosion Risk:
If not correctly coated or treated, steel fibers may be susceptible to corrosion over time, potentially compromising the integrity of the concrete structure.
- Handling Challenges:
Incorporating steel fibers into concrete mixtures can present challenges in terms of mixing, placement, and finishing, requiring specialized equipment and expertise.
- Uniform Distribution:
Ensuring the uniform distribution of steel fibers throughout the concrete matrix can be difficult, which may lead to variations in mechanical properties and performance.
Final Verdict:
Steel fiber reinforcement plays a crucial role in enhancing concrete structures’ mechanical properties and durability. By understanding the different types of steel fibers available, their manufacturing process, and their applications in concrete construction, engineers and designers can effectively utilize this technology to create resilient and long-lasting infrastructure. As advancements in material science continue, the development of innovative steel fiber products promises further improvements in the performance and sustainability of concrete structures.