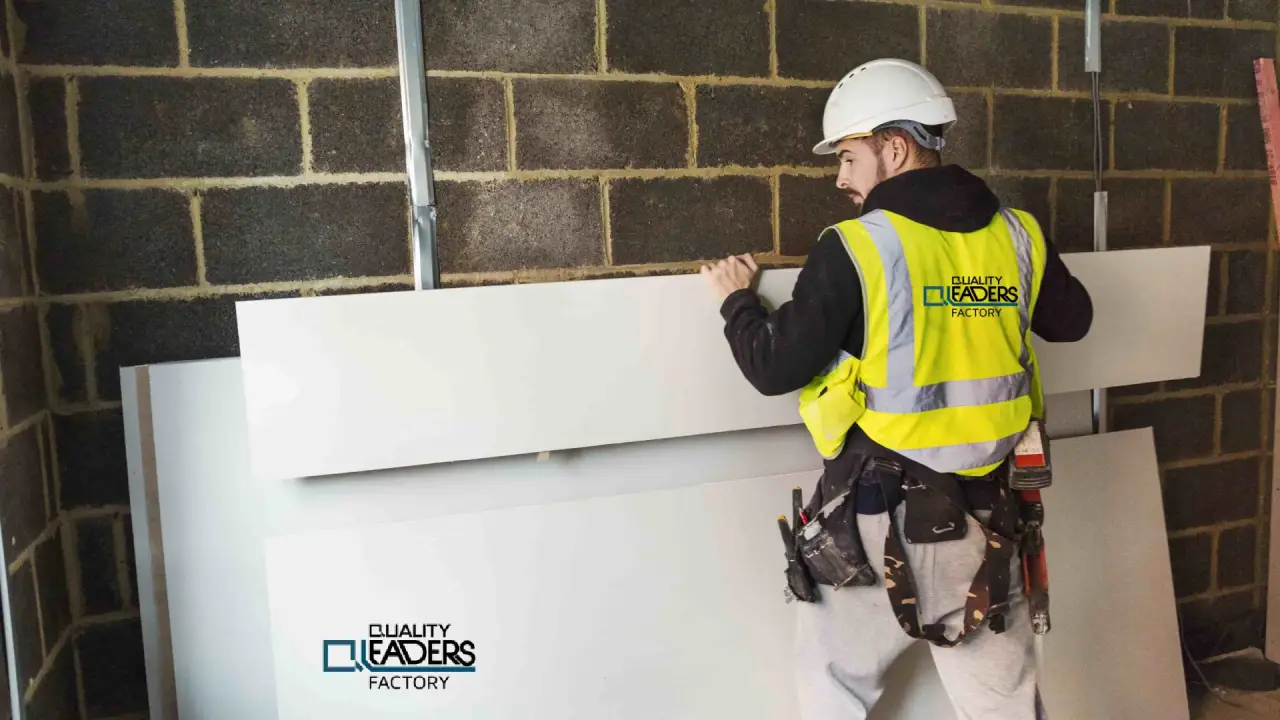
What are the Uses of Sandwich Panels in Buildings: Revolutionize Architecture
Introduction:
Hey there, fellow construction enthusiasts and proficient architects; today, I have brought this informational article that will give a more profound and better insight into sandwich panels and the use of Sandwich Panels in buildings. Sandwich panels are game changers in the construction of the modern world. Sandwich panels have revolutionized the construction process, from crafting a sustainable and cozy place for the family to making a sleek office space on a small budget to enhance productivity. The sandwich panel will get you covered.
Sandwich panels have three layers: a low-density core and a thin skin layer bonded.
Properties of Sandwich Panels:
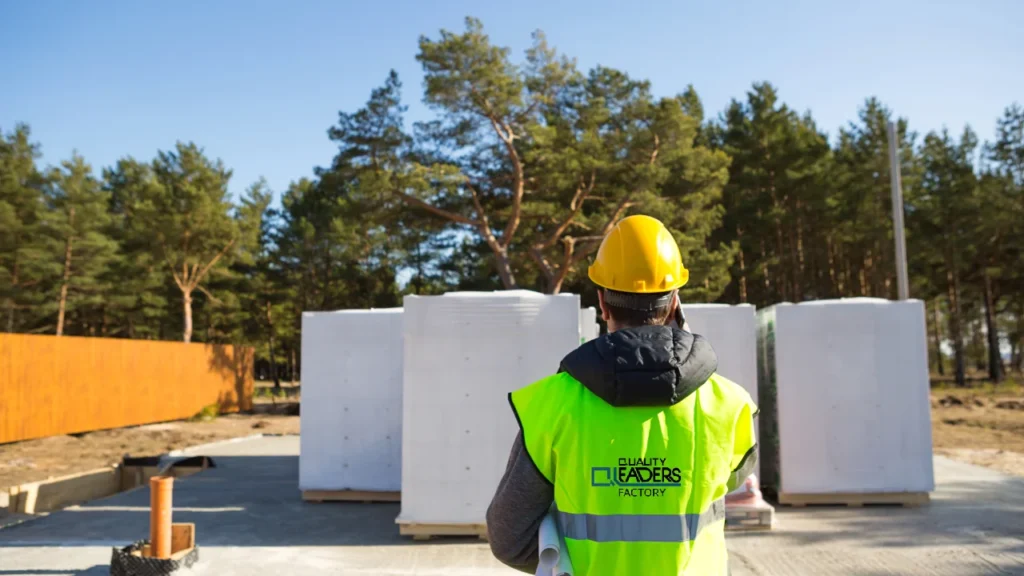
Several properties and characteristics make the sandwich panels perfect for contemporary modern construction projects at every level. Let us highlight these properties that make them a Favorite choice in the construction world.
Light Weight:
Due to the lightweight use of sandwich panels in buildings, it is inevitable. This lightweight property makes the installation process quick and easy.
Customization:
Sandwich panels have the property of customization. You can alter it to suit the particular requirements of your structure and the surrounding environmental and physical factors. You can choose the size, thickness, and finishes according to your requirements.
Durability:
The outer protective sheets make the sandwich panels highly durable and resistant. Outer metallic sheets are fire and UV-radiation-resistant.
Acoustic Insulation:
Acoustic insulation makes these sandwich panels noise-resistant, resulting in zero noise pollution. It enhances focus by providing a peaceful environment.
Low Thermal Conductivity:
They have maximum thermal insulation resulting in low heat transfer, especially in summer this feature protects against scorching sun anger.
Impermeable:
Different chemicals and methods keep the sandwich panels impervious to water, snow, steam, etc. This feature makes them a safer choice.
Types of Sandwich Panels According to their Application:
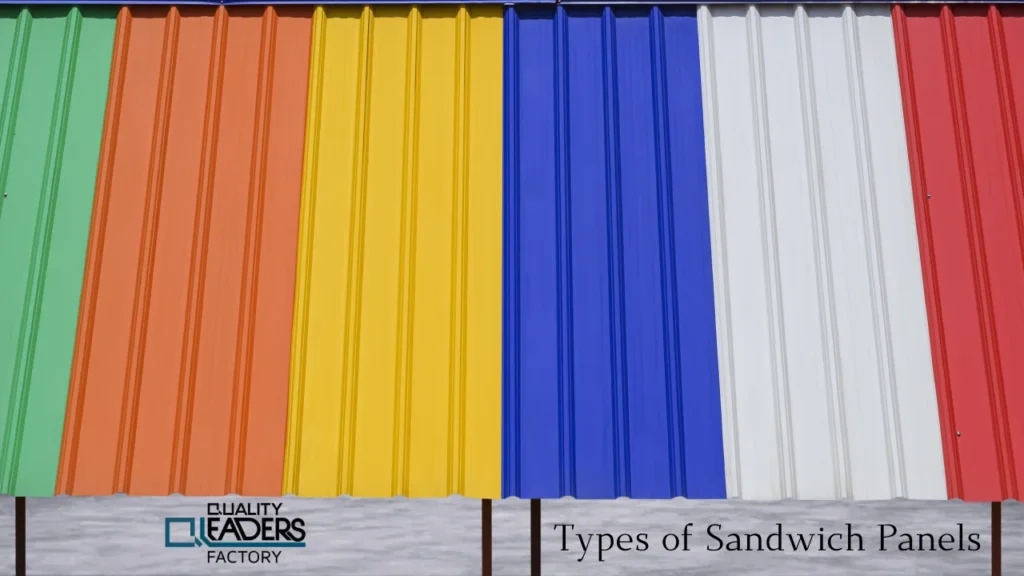
Sandwich Panels for Facades:
Sandwich panels for facades are specifically designed for the outer cladding or facade of buildings. They prioritize aesthetics, weather resistance, and architectural appeal. Sandwich panels for walls may have a more straightforward design and fewer aesthetic options since they are often concealed within the building structure.
Sandwich facade panels typically come in more diverse finishes, textures, and colors to enhance the building’s exterior appearance. They may also incorporate features like concealed fastening systems for a seamless look. They undergo additional weatherproofing coatings and treatments to withstand rain, wind, and ultraviolet radiation.
Sandwich Panels for Roofs:
Sandwich panels used in roofing systems are different from faced sandwich panels. These panels are manufactured according to sandwich panel roofing specifications and installed differently. They are manufactured in a way to prevent water leakage and humidity. Self-drilling screws along with sealing joints are present, which make them easy and flawless installation without damaging the insulation layers.
Sandwich Panels for Refrigeration:
Sandwich panels for refrigeration and cold rooms are also available. These refrigerated panels use thick insulation, which keeps the temperature low within a narrow range. Joints are also manufactured and attached precisely to maintain lower internal temperatures.
Sandwich Panels for Walls:
Sandwich panels for walls are designed for use in exterior and interior buildings. They are available in a range of dimensions, coatings, and thicknesses. Wall panels are manufactured to provide insulation, structural support, and acoustic properties, offering flexibility to meet different design and construction requirements.
What Are the Types of Sandwich Panels:
Metal Faced Sandwich Panels:
Sandwich panels with a metal face are frequently utilized in commercial, residential, and industrial building constructions. They provide the best thermal insulation, durability, protection, and strength against harsh environmental conditions. These panels have metallic sheets outside. Usually, steel or aluminum is used in these metallic sheets. Mineral wool is sandwiched between these metallic layers with a polyurethane (PUR) core substance and polyisocyanurate (PIR). Due to metallic sheets, this type is durable and robust.
Fibreglass Faced Sandwich Panels:
Fiberglass-faced sandwich panels are known for their corrosion-resistant properties. These lightweight sandwich panels have various core material options. Due to their corrosion resistance, they are mainly used in the manufacture of marine and offshore structures.
Wood Faced Sandwich Panels:
These wood-faced sandwich panels are primarily used in residences, buildings, or office settings where an aesthetic look and functionality are desired. They are used primarily in partitioning. The external sheets of sandwich panels are made of wood, and the core material may consist of foam or wood-based products.
Composite Sandwich Panels:
These sandwich panels are used in aerospace and automotive. They have an outer layer of carbon fiber or fiberglass. In the center of these outer sheets is a honeycomb-core foam.
Insulated Concrete Sandwich Panels:
Mineral-faced Sandwich panel:
These sandwich panels consist of metal or any other material. The core of this kind of sandwich panel is different, as it is made of minerals. The mineral wool used in this mineral wool-faced sandwich panel is fire-resistant and has acoustic-proofing capabilities. These properties make mineral wool especially eligible to be used in high-security areas with a soundproofing punch.
Life Span of a Sandwich Panel:
Sandwich panels are composed of metal surfaces that are filled with insulation material.
The sandwich panel’s outer sheet or metal surface is designed to resist high-temperature thermal radiation, ultraviolet radiation, and external environmental effects. The sheet is also designed to resist chemical effects and withstand physical and condensation processes.
The durability and longevity of sandwich panels depend heavily on the protocols and precautions you follow during installation. The sandwich panel must be chosen according to the building’s needs and demands, considering the climate and environmental conditions. While selecting the perfect sandwich panel, make sure that the load-carrying capacity of these panels matches and is well calculated according to the type of the building.
Another important factor that enhances the life span of a sandwich panel is its maintenance and cleaning. It is necessary to fix the damages and to clean these sandwich panels at least once a year.
Sandwich Panel Price in Saudi Arabia:
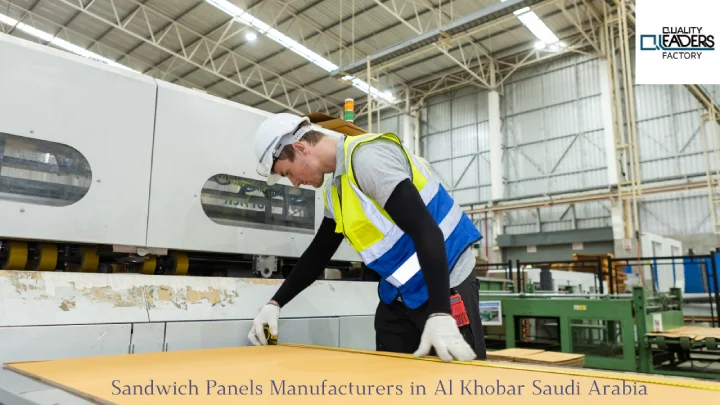
Sandwich panel prices in Saudi Arabia vary based on the quality of sandwich panels, the material used, the thickness, and the customization options. The price range in the recent market of Saudia is SAR 50 to SAR 150 per square meter for standard sandwich panels. But this is not the fixed price; it varies depending on the quality of materials, brand reputation, customization options, and market demand. It’s advisable to contact local suppliers or Sandwich panel manufacturers in Saudi Arabia directly for accurate pricing information. It is tailored to your specific requirements. You can choose according to your particular requirements.
Wrapping up: What are the Uses of Sandwich Panels in Buildings:
In conclusion, sandwich panels play a crucial role in contemporary modular building construction. They bring versatile, convenient, and quick solutions to complicated problems. These sandwich panels are a popular choice at every level, from residential to commercial and business, as they enhance aesthetic appeal with quick installation and economy.
FAQs:
What are PU Sandwich panels Used for?
In the construction of buildings, PU sandwich panels are frequently utilized for structural and insulating purposes. These panels provide exceptional thermal insulation qualities, perfect for walls, roofs, and ceilings in residential, commercial, and industrial structures. They have a polyurethane (PU) foam core sandwiched between metal or rigid facings.
They are also a well-liked option for expedited construction projects due to their lightweight design and simplicity of installation. Their thermal efficiency, durability, customization options, and cost-effectiveness make them a preferred choice for architects, builders, and property owners, contributing to sustainable and resilient built environments.
Is the sandwich panel good?
Yes! Sandwich panels are a good choice for the construction of buildings, as they are economical, light in weight, having the best insulation properties with easy and quick installation. Sandwich panels are used in various commercial, residential, and industrial projects, such as constructing walls, roofs, and facades. Sandwich panels are popular due to their customization options in modern buildings. Moreover, they resist fire, water, heat, and air inflation, ensuring longevity.
What is a sandwich in construction?
A “sandwich” in construction usually refers to a multi-layered structural panel. Sometimes referred to as skins or facings, these layers typically consist of a core material sandwiched between two exterior layers. The core material can be made of various materials, such as concrete or wood, or insulated with foam or mineral wool. Sandwich panels are frequently used in construction because of their strength, insulation, and adaptability for various applications, including floors, walls, and roofs.
What is a sandwich panel structure?
A sandwich panel structure has three layers: a core material sandwiched between two exterior layers, or skins, and a structure. Rigid materials like metal or fiberglass are usually used for the exterior layers, and a variety of materials, including foam or mineral wool for insulation, are used for the core. Sandwich panels are frequently employed in constructing walls, roofs, and floors because of their strength, insulating qualities, and adaptability.