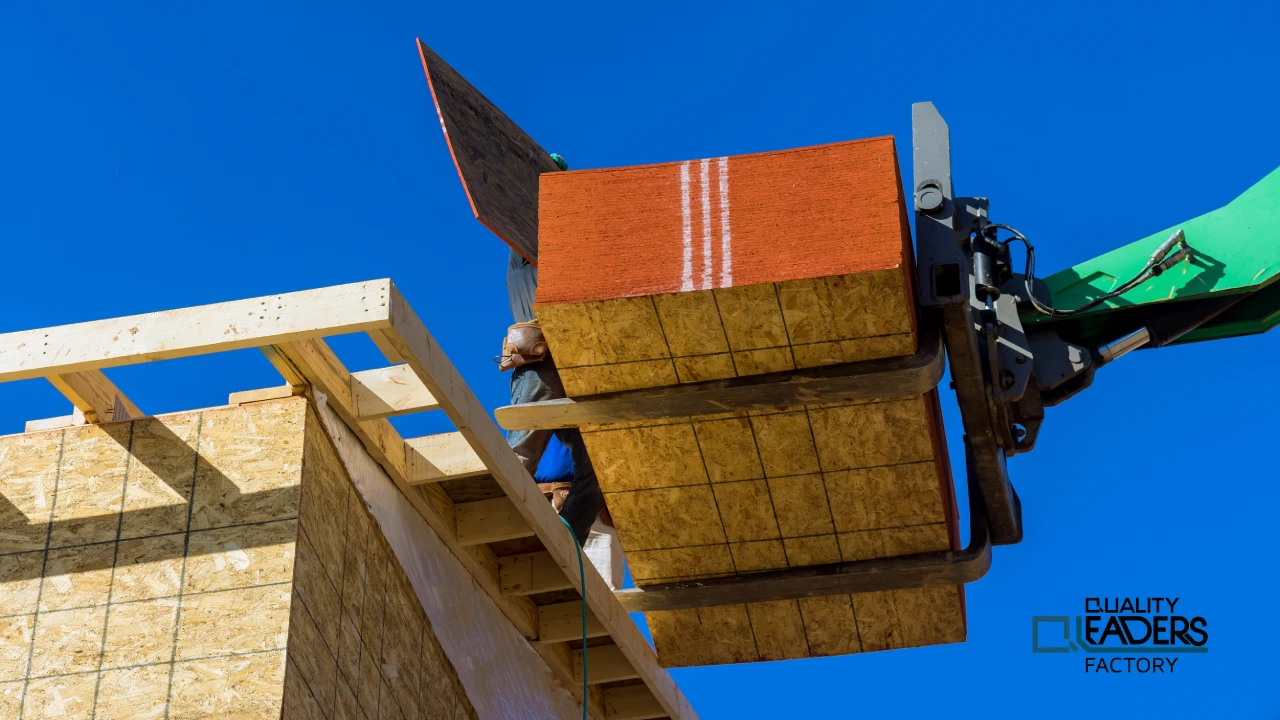
Use of Sandwich Panels in Construction: Benefits, Sizes, Installation Tips
What is a Sandwich Panel in Construction?
Sandwich panels are advanced construction materials that offer efficient solutions for insulating and protecting buildings. They consist of a core layer of insulation sandwiched between two outer layers of high-density material such as metal or plywood and are renowned for their lightweight yet durable properties.
They are prefabricated, which speeds up construction times and helps reduce overall costs. Due to their design, sandwich panels excel in thermal insulation, soundproofing, and weather resistance, making them ideal for various building applications.
These versatile panels are commonly used in industrial and commercial settings, including factories, warehouses, and cold storage facilities. Their ability to provide significant thermal insulation helps maintain comfortable internal temperatures and reduces energy costs. Sandwich panels are also used in residential buildings and agricultural structures due to their effective insulation properties and strength.
The choice of insulation material within the panels—such as PUR, PIR, Mineral Wool, or EPS—depends on specific needs such as thermal efficiency, humidity control, soundproofing, and fire resistance. This flexibility allows for tailored solutions that meet diverse project requirements. Additionally, sandwich panels are advantageous for their high strength-to-weight ratio, contributing to the construction’s durability and efficiency.
Overall, sandwich panels represent a modern approach to building construction, combining practicality with performance. They are used in various applications, from roofing and cladding to internal walls and cold storage, making them a valuable asset in contemporary building practices.
What is the Purpose of the Sandwich Panel?
Sandwich panels are versatile construction materials that enhance buildings’ structural integrity and insulation. Comprising three layers—a durable exterior, an insulating core, and an interior layer—these panels offer practical solutions for heat, sound, and moisture control.
The core material, typically foam, contributes to the panel’s lightweight yet sturdy properties, making them ideal for walls, roofs, and floors. Due to their durability and efficiency, these panels are especially prevalent in commercial and industrial settings like warehouses and factories.
In addition to their primary applications, sandwich panels are employed in various other building scenarios, including food refrigeration units, agricultural facilities, and livestock shelters. Their adaptability extends to replacing roofing sheets, constructing canopies, and creating sheds and warehouses.
This broad range of applications highlights the panels’ ability to provide cost-effective and reliable solutions across different construction sectors.
Why is it called a Sandwich Panel?
The term “sandwich panel” originates from the panel’s construction, which resembles a sandwich with three distinct layers. The outer layers are generally crafted from durable materials like metal, while the core layer consists of insulating substances such as foam. This arrangement enhances the panel’s ability to provide thermal insulation and structural support, as a sandwich has different layers to combine flavors and textures.
The “sandwich” design allows these panels to effectively combine strength and energy efficiency. These panels deliver improved thermal performance and durability for various building applications by sandwiching an insulating core between two robust outer layers. This layered approach contributes to better insulation and makes the panels an efficient choice for modern construction, reducing energy consumption and material costs.
What Do I Need to Know About Sandwich Panel Installation?
Essential Tools and Materials
Before beginning the installation of sandwich panels, ensure you have all the necessary tools and materials. This includes a building level to check panel alignment, a drill or screwdriver for fastening, and a cutting knife for size adjustments and openings. Other essential items are a hammer for additional force, pliers for precise cuts, and sealing materials like gaskets and tape to prevent water and air infiltration.
Installation Workflow
The installation process should start with carefully placing the first panel, using fasteners that penetrate its total thickness. Subsequent panels must be aligned and pressed firmly to maintain tight joints and prevent thermal bridging. Using vacuum lifts to handle the panels is recommended to ensure safety and efficiency during installation.
Preparatory Steps
Proper preparation is crucial for a smooth installation. Develop a detailed plan for panel placement and ensure that design and installation documentation is complete. This includes layout plans, attachment method information, mounting elements, and seal specifications.
Adhering to Technology and Procedures
Following established installation procedures is vital for achieving optimal performance and durability. Correct installation techniques ensure aesthetic appeal, adequate insulation, and resistance to environmental factors. Before starting panel assembly, complete all preliminary work, such as checking structural compliance and applying anti-corrosion coatings.
Handling and Placement
Panel transport and lifting should be managed to minimize damage and ensure ease of installation. Scaffolding should be appropriately set up, with a minimum width of 2.5 meters between scaffolding and load-bearing structures. This careful handling prevents mechanical damage and facilitates efficient panel placement.
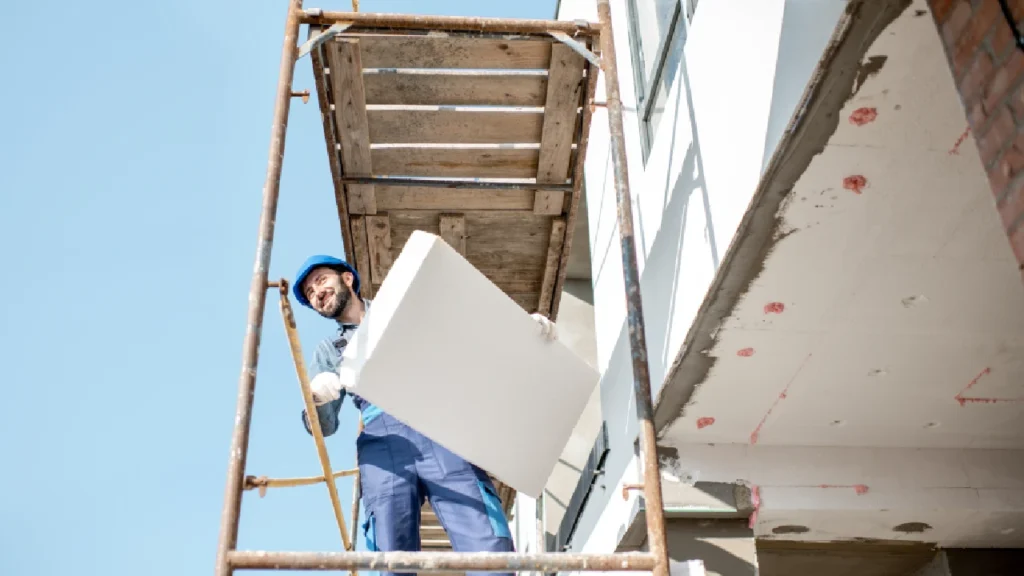
Advantages of Sandwich Panels
Fast and Efficient Installation
Sandwich panels streamline construction by arriving at the site as fully assembled and ready-to-install components, customized to meet specific dimensions and insulation requirements. This pre-fabrication significantly reduces on-site assembly time, allowing projects to be completed more quickly than traditional methods.
Additionally, the ease of handling and transporting these panels, aided by advanced lifting equipment, further accelerates the installation process.
Superior Thermal Insulation
Sandwich panels provide thermal insulation through a core of materials such as PUR, PIR, EPS, or Mineral Wool. This effective insulation minimizes energy costs by reducing the need for heating and cooling while preventing mold and moisture-related issues. The insulation material and panel thickness can be adjusted based on building needs and local climate conditions.
Cost-Effective Investment
Utilizing sandwich panels can lead to substantial savings in both construction and long-term maintenance costs. Their ease of installation and ability to be disassembled and reused make them ideal for renovations and expansions. Furthermore, the lightweight nature of these panels reduces transportation and structural costs, enhancing overall economic efficiency.
Aesthetic Versatility
Sandwich panels are available in various colors and finishes, allowing multiple design possibilities to enhance a building’s appearance. Their ability to be installed in different orientations—horizontally, vertically, or angularly—provides additional flexibility in architectural design. This adaptability helps in achieving both functional and visually appealing building facades.
High Fire Resistance
Choosing the right sandwich panel can significantly enhance a building’s fire safety. Panels with core materials such as Mineral Wool or FM-approved PIR offer excellent fire resistance, helping to slow down the spread of flames and protect the building. Selecting panels based on the specific fire resistance requirements and building specifications is crucial.
Excellent Air and Water Tightness
The precise joint details of sandwich panels ensure adequate air and water tightness, preventing leaks and maintaining consistent thermal insulation throughout the building. This feature enhances energy efficiency by minimizing heat loss and guarding against water damage from external weather conditions. As a result, the building becomes more durable and comfortable, with reduced risk of mold and corrosion.
Effective Sound Insulation
Sandwich panels provide excellent soundproofing due to their mineral wool insulation core and perforated surface options. This capability helps create quieter, more productive environments by minimizing noise transmission. This improves workplace conditions and reduces noise-related disruptions in commercial and industrial settings.
Durability and Longevity
The robust materials used in sandwich panels, such as galvanized metal, ensure durability and longevity, making them a reliable choice for building exteriors. Their resistance to impact, weather conditions, and wear helps maintain the structural integrity of the building over time. The panels’ ease of maintenance and cleaning also contributes to their long-term performance.
PUR Panels and PIR Panels
Overview of PUR and PIR Panels
PUR (polyurethane foam) and PIR (polyisocyanurate foam) panels are sandwich panels renowned for their thermal insulation capabilities. These panels are designed to be lightweight and provide significant energy efficiency by reducing heating and cooling needs. Despite their similar chemical backgrounds, PIR panels generally offer superior fire resistance compared to PUR panels.
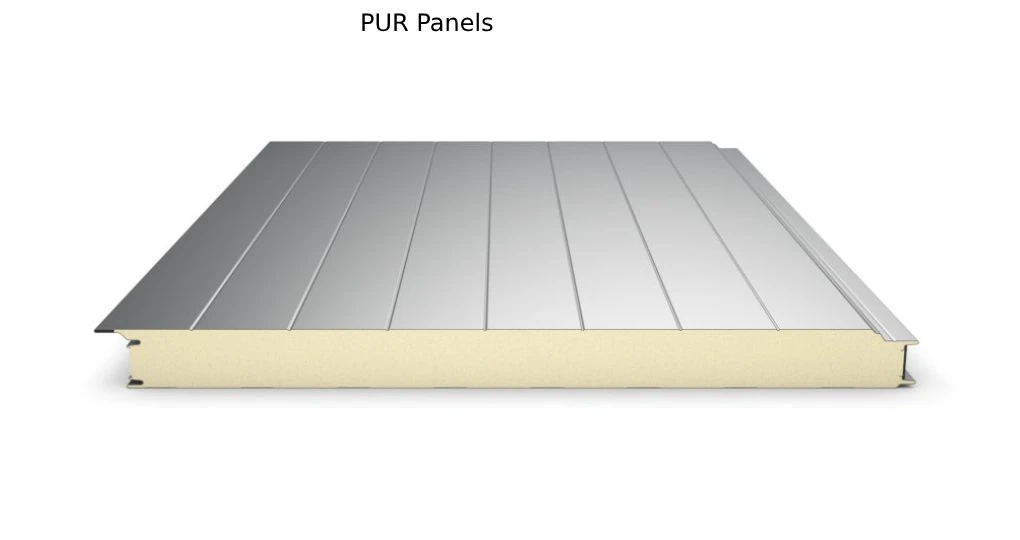
Manufacturing and Environmental Impact
Synthesia Technology has used recycled PET and polyester polyols in PIR panel production since 2003, emphasizing sustainability and circular economy principles. This approach supports ecological practices and ensures that the materials are recyclable and environmentally friendly. Such innovations reflect a commitment to reducing the environmental footprint of construction materials.
Chemical Composition and Performance
The chemical processes of creating PUR and PIR foams are distinct yet related. PUR panels are formed through the reaction of polyol and isocyanate components, producing urethane linkages. In contrast, PIR panels undergo trimerization reactions among isocyanates to form isocyanurates, enhancing fire performance and producing urethane linkages.
Application and Use Cases
PUR and PIR panels are versatile and used in various construction applications, including external enclosures like facades and roofs and interior compartmentalization in fire sectors and cold rooms. Although the application fields for both types of panels are similar, the choice between them often depends on specific performance requirements, such as fire resistance. These panels create energy-efficient, well-insulated buildings across diverse industrial and commercial settings.
Sandwich Panel in Warehouses and Its Fireproofing
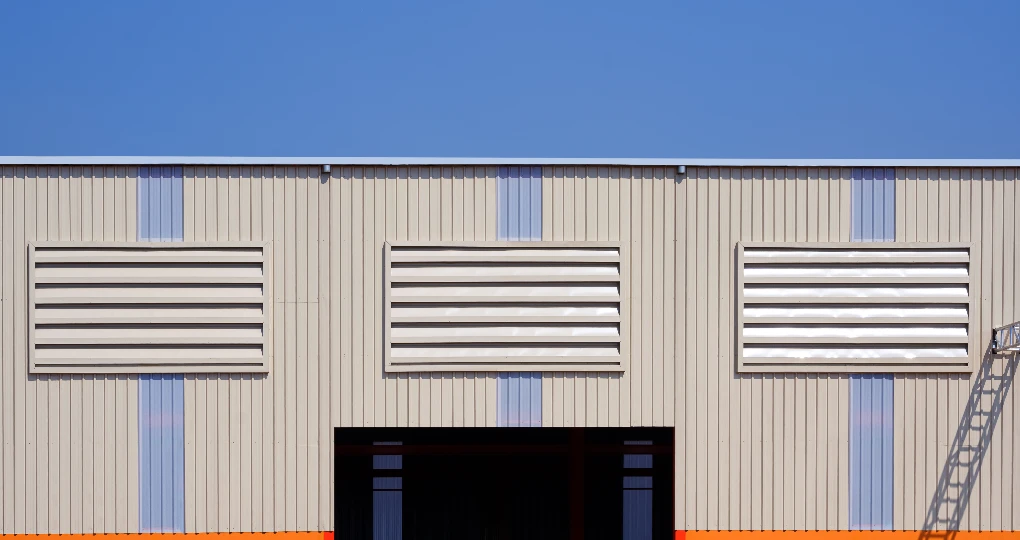
Sandwich Panels in Warehouses
Sandwich panels are increasingly used in warehouse construction due to their excellent thermal insulation and structural benefits. Their lightweight nature and ease of installation streamline the building process, allowing for faster project completion. Additionally, the panels’ ability to maintain consistent internal temperatures helps protect stored goods and reduce energy costs for climate control.
Fireproofing with Sandwich Panels
Fireproofing is critical to warehouse safety, and sandwich panels can be engineered to enhance fire resistance. Panels with PIR (polyisocyanurate) cores are particularly effective in delaying the spread of flames, thanks to their superior fire-resistant properties. By integrating these fire-resistant panels, warehouses can achieve better protection for the building structure and the inventory inside, ensuring compliance with safety regulations and minimizing risk.
Sandwich Panels in Industrial Warehouse Construction
Sandwich panels offer a practical solution in industrial warehouse construction due to their strong insulation properties and quick installation. These panels, with their core of insulating material sandwiched between two durable outer layers, provide excellent thermal performance, which helps regulate internal temperatures and reduce energy costs. Their lightweight design simplifies transportation and assembly, making them ideal for large-scale warehouse projects that require efficiency and cost-effectiveness.
Benefits for Industrial Warehouses
Sandwich panels are also valued for their durability and low maintenance requirements, which are crucial for the demanding environment of industrial warehouses. The panels’ resistance to weather, corrosion, and physical wear contributes to longer service life and lower upkeep costs. Additionally, their versatility allows easy customization to fit various architectural designs and functional needs, further enhancing their suitability for diverse industrial applications.
How Big is a Sandwich Panel?
Typical Dimensions
Sandwich panels generally have a standard width of 1,000 mm or sometimes 1,150 mm. Their length is highly adaptable, with standard sizes ranging from 3 to 6 meters, though they can extend up to 16 meters for specific projects. Panel thickness varies significantly based on the intended use, typically between 40 mm and 200 mm.
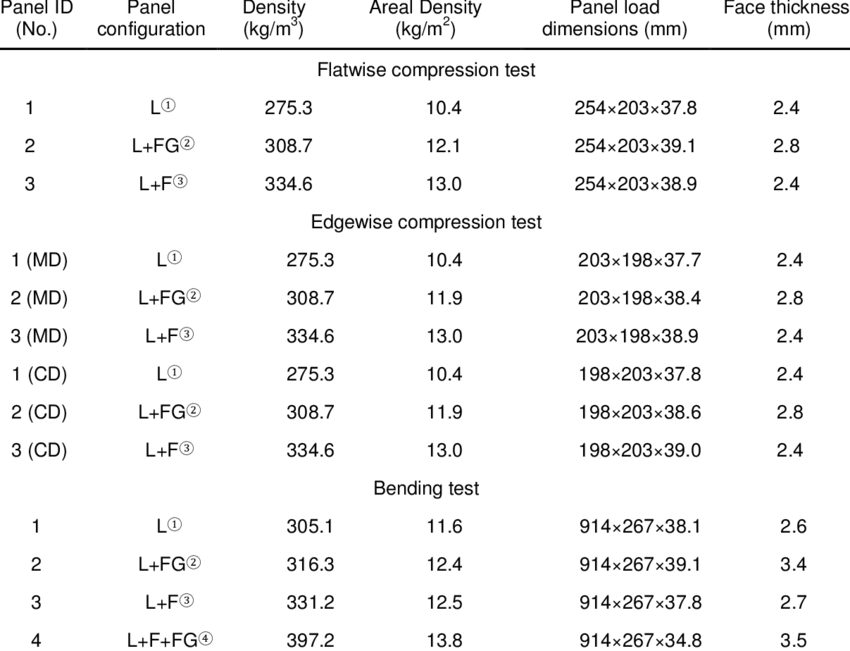
Customization and Manufacturing
There are no strict industry standards for sandwich panel dimensions, allowing considerable customization to fit specific project needs. While standard sizes are widely available, custom sizes can be ordered from many manufacturers, though this might increase the cost per square meter. Custom panels may reduce waste and lower overall costs if the project requirements are carefully calculated.
Considerations for Ordering
When ordering sandwich panels, it’s essential to distinguish between “working” or “useful” width and the overall dimensions, which often include additional space for panel locks. The actual panel size might be slightly larger than the listed dimensions. Each manufacturer has its range of available sizes, so checking with suppliers for specific capabilities and limitations is advisable to ensure the right fit for your project.